Ensuring Building Integrity: How to Spot and Address Construction Defects Effectively
Maintaining building integrity requires vigilance against construction defects. Identifying and effectively addressing these issues in a building project not only guarantees safety but also preserves your building’s structural health. If you’re looking to spot warning signs and implement solutions, our comprehensive guide on “building integrity: how to spot and address construction defects” walks you through the process, ensuring your construction stands solid and secure.
Understanding the Pillars of Building Integrity
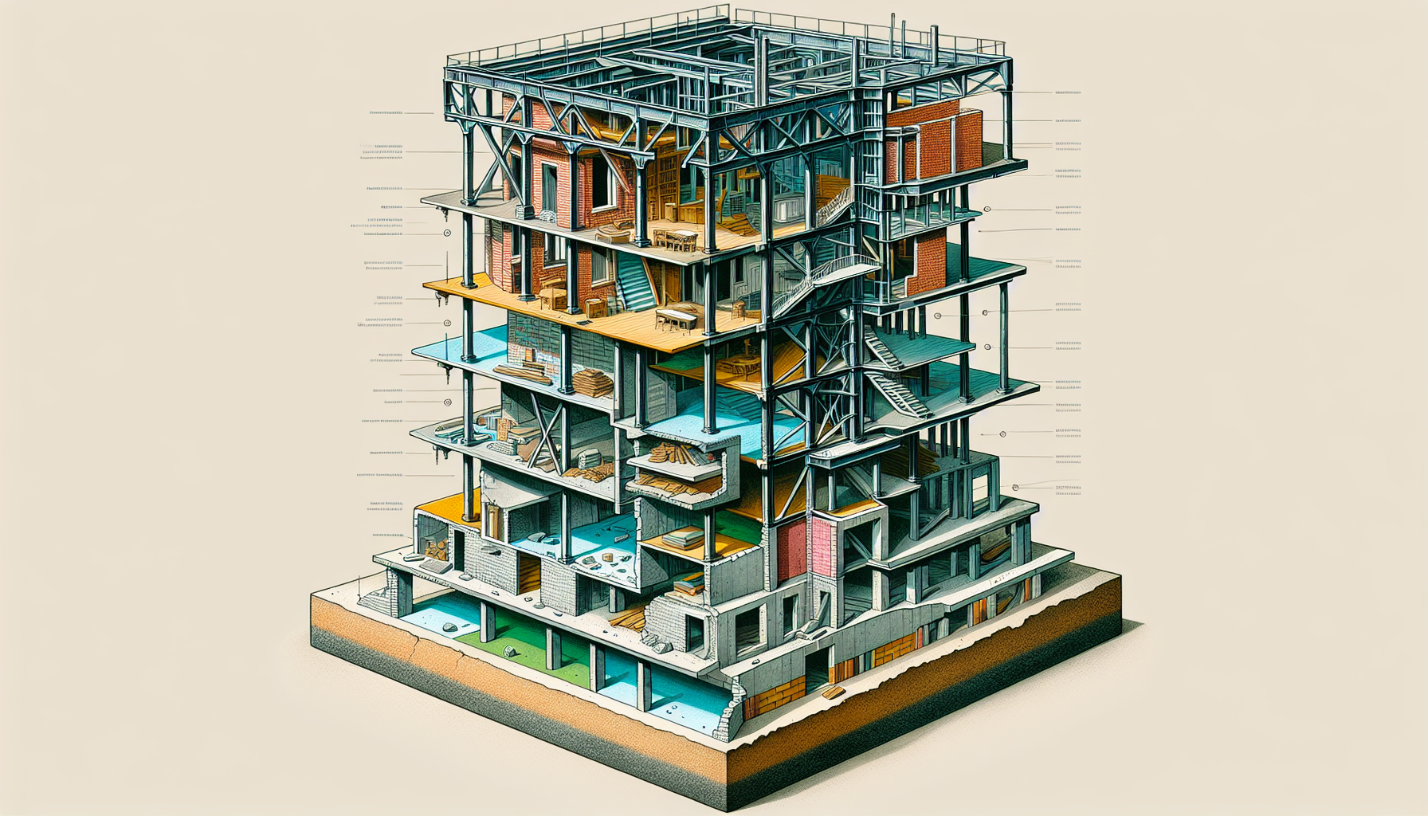
The stability of construction is comparable to a tripod, supported by three fundamental aspects: structural integrity, compliance with building codes, and the caliber of materials used. Each aspect holds equal importance. If any are compromised, it may result in an insecure and unsteady edifice.
At its core, structural integrity supplies the foundational strength that ensures resilience over time for the structure. The role of building codes is akin to that of a safety handbook which safeguards during both the construction process and while buildings are inhabited. Meanwhile, selecting high-quality materials plays an essential part in warding off defects related to construction as they lend themselves directly to how durable a structure will be. Understanding construction defects is crucial as it forms the first step in managing and preventing these issues, thereby maintaining building integrity.
To appreciate these components more fully, let’s examine each one closely.
Structural Integrity: The Foundation of Integrity
A building’s foundational strength is as crucial to its structural integrity as roots are to a tree’s stability. A durable foundation and strong structure signify a secure and stable edifice. Nevertheless, signs of foundation issues like cracks or an uneven base may give rise to structural instability, endangering the safety of occupants. If left unattended, these structural defects could cause harm to the whole structure.
Thus, upholding a building’s structural soundness is imperative for preserving both its longevity and overall integrity.
Adherence to Building Codes: Ensuring Safety Standards
Envision building codes as a comprehensive set of guidelines that dictate how structures should be designed, built, modified, and preserved. These regulations act like vigilant protectors in the construction arena, safeguarding occupant well-being and public health. As reliable guides, they continuously update to include modern safety requirements, technological advancements, and improved construction methods that mirror progress within the industry.
These codes take into account local environmental factors and hazards by offering region-specific protections. Fundamentally speaking, building codes quietly play a pivotal role—they are instrumental in reducing construction defects while enhancing overall safety protocols.
Quality of Materials: A Cornerstone in Construction
Imagine building edifices with inferior building materials – akin to assembling a fragile house of cards prone to crumble from the slightest nudge. The essence of preventing construction defects and bolstering longevity lies in utilizing high-grade materials. From incorporating windows that hinder air leaks and block moisture penetration, employing vapor barriers safeguarding flooring and framing structures, selecting top-tier insulation for heightened energy conservation, to opting for robust roofing substances offering defense against climatic conditions – each material contributes significantly.
Fundamentally, opting for superior quality materials is comparable to handpicking premier bricks that lay the foundation of an impregnable fortress destined to withstand eras unyieldingly.
Identifying Signs of Construction Defects
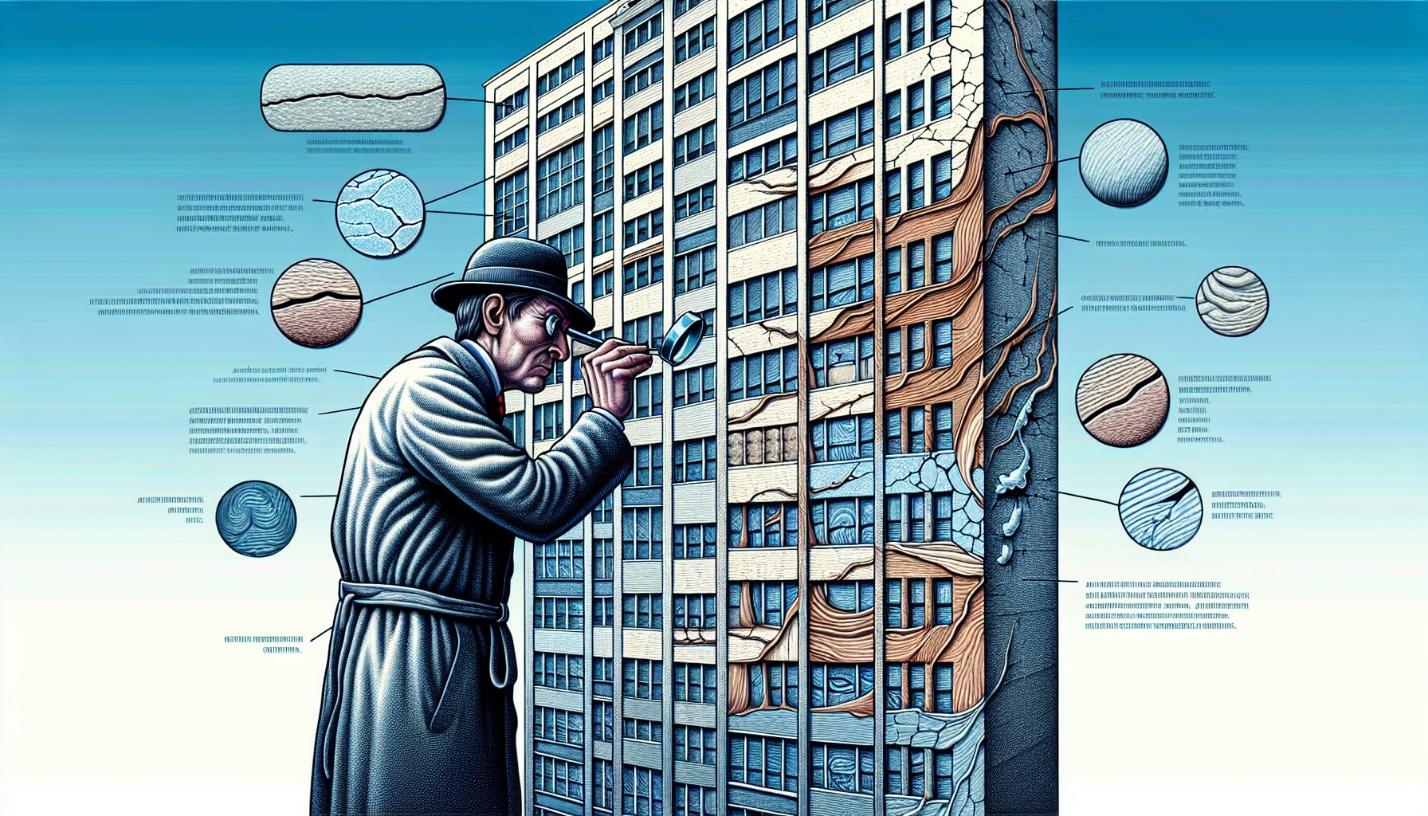
Imagine yourself as a sleuth tasked with unearthing various construction defects that could compromise the structural integrity of a building. Construction defects are imperfections or shortcomings in the design, craftsmanship, or materials used in a building project. Pinpointing occurrences of these construction flaws is crucial for their proper management, ensuring safety, and circumventing costly fixes. Construction defects encompass an array of problems such as:
- Issues with foundations
- Intrusion by water
- Deficiencies in structure
- Mistakes in design
Each presents its distinct set of obstacles.
So what’s our strategy for detecting these imperfections? It’s time to don our detective caps and investigate further.
Visual Inspections: What to Look For
The initial step in identifying construction and material defects is a visual inspection. This can uncover clear indications of structural issues, including cracked walls, sagging floors, or doors and windows that don’t line up properly. Visible signs of moisture buildup and water damage can also be the result of improper installation, leading to air leaks and moisture intrusion. Discoloration on surfaces might suggest deeper hidden problems while noticeable seams in countertops and cabinetry may point to surface defects.
Attention to detail is crucial as subtle hints often reveal these concealed imperfections. A vigilant observer can detect such inconspicuous signals indicating potential problems with the construction or materials used.
Professional Assessments: When to Call an Expert
Visual assessments are vital, yet they only reveal so much. Often the severity of a flaw extends beyond what can be detected by simple observation. In such cases, it’s the skill and knowledge of construction professionals that becomes essential.
These specialists can provide a detailed and precise evaluation of any deficiencies present, enabling an efficient path to remediation.
Diagnostic Tools and Techniques
In this era of technology, experts have access to sophisticated instruments that allow them to identify construction defects without inflicting damage on the building elements. Thermal imaging is used to evaluate possible structural issues and drones are employed for precise and efficient construction site inspections. These advanced diagnostic methods not only assist in pinpointing construction flaws but also facilitate their successful resolution.
Addressing Common Construction Defects
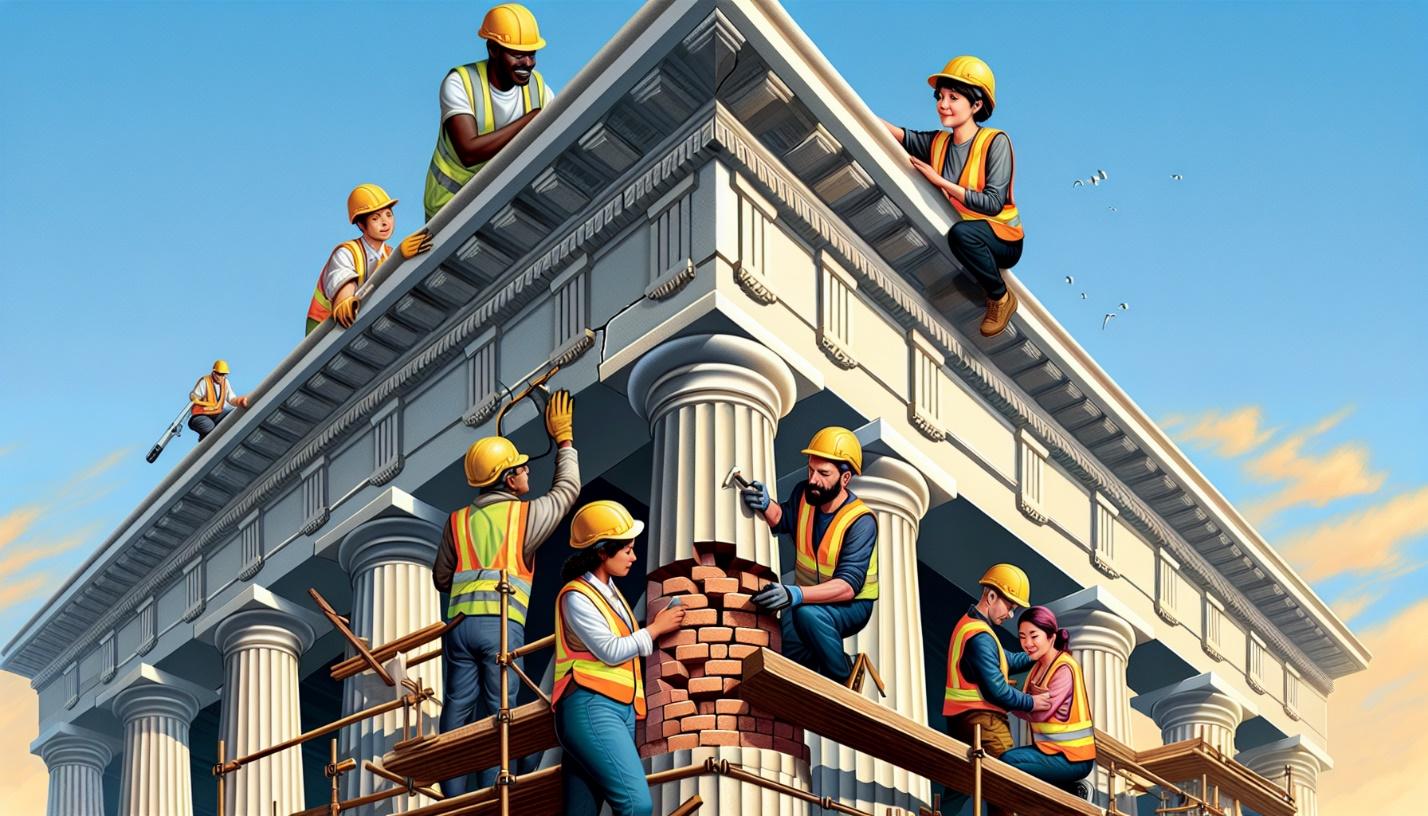
When discussing construction projects, it's essential to understand the various types of construction defects, such as structural issues, water intrusion, and electrical/plumbing flaws.
Spotting construction defects is only half the battle. The second, equally crucial part involves swift corrective action to ensure safety, avert additional harm, and protect investments. From addressing structural issues to resolving water intrusion or fixing problems with electrical and plumbing systems—each type of defect necessitates a tailored solution for successful resolution.
Now let’s explore these solutions in detail.
Tackling Structural Issues
Addressing structural issues promptly and efficiently is essential for maintaining the integrity and safety of a building. Whether dealing with foundational problems that cause cracking and instability or devising repair strategies in response to natural disasters such as earthquakes or hurricanes, each issue demands its own tailored solution.
Despite the high expense associated with restoration, it is vital to reinstate a building’s inherent structural integrity. Doing so not only guarantees security but also wards off the possibility of even more costly repairs down the line.
Remedying Water Intrusion and Moisture Problems
The integrity of a building can be steadily eroded by water intrusion and issues related to moisture, similar to how termites quietly undermine the structure’s foundation. To combat these challenges and avoid damage, it is essential to put in place robust waterproofing techniques and efficient seepage control systems.
Taking steps such as correcting water entry caused by incorrectly installed windows or defective roofs, as well as properly fitting exterior penetration flashing, each serves an important role in extending the lifespan of the edifice.
Correcting Electrical and Plumbing Flaws
Defects in functionality, such as issues with plumbing or electrical systems that are not readily apparent, can greatly impede the efficiency and safety of a structure. The design and installation of mechanical and electrical systems need to be accurate. Addressing any operational shortcomings swiftly is crucial to preserve integrity and prevent safety risks.
Preventive Measures and Quality Control
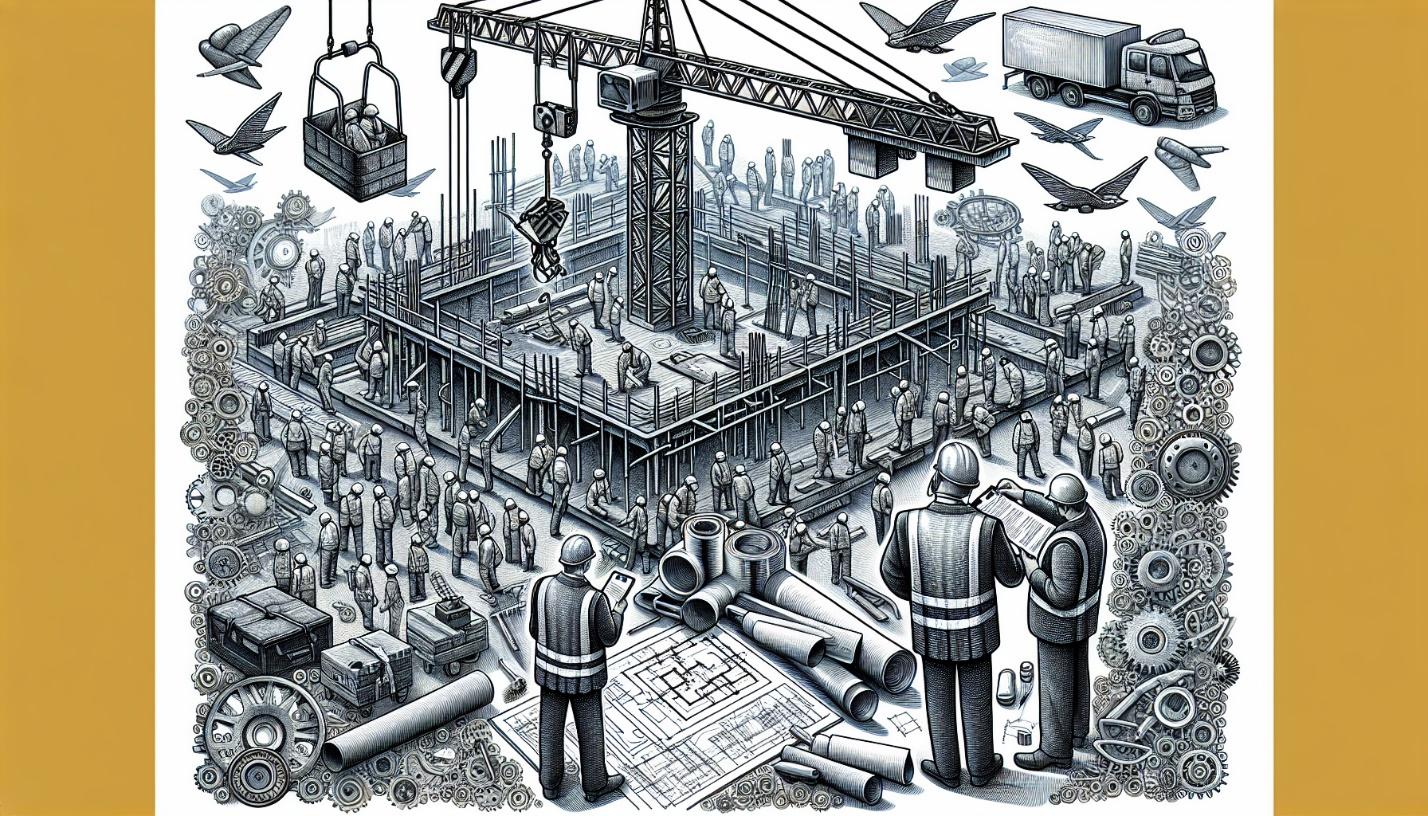
To achieve construction without defects and maintain high standards, it is crucial to focus on preventive strategies and quality control measures that are aimed at minimizing construction defects. Implementing regular inspections, strictly following design specifications, and utilizing technology can all play significant roles in averting issues such as finishing and waterproofing flaws.
Implementing Stringent Quality Assurance Protocols
Acting as a vigilant protector, quality assurance meticulously supervises the construction process to ensure that each phase unfolds seamlessly and adheres to established standards. Through rigorous enforcement of strict quality protocols, conducting consistent audits, and scheduling systematic inspections, it allows for the early detection and resolution of potential problems, effectively curtailing expenses associated with repair work.
Regular Maintenance: A Proactive Approach
Performing routine upkeep acts as a health assessment for the structure, averting major harm and extending the durability of machinery. Every chore, ranging from changing oil to establishing energy standards for HVAC systems, plays a role in the continual enhancement of quality.
Educating Construction Teams
Ensuring that a construction project is successful hinges on the expertise of an informed team. Initiating training initiatives and requiring certification for operating specialized machinery can help preserve uniform quality and compliance with established norms in every building endeavor. Routinely assessing subcontractors is critical in reducing occurrences of construction defects significantly.
Navigating Legal Aspects of Construction Defects
Understanding contracts, warranties, and dispute resolution processes is essential in effectively navigating the intricate legal terrain of construction defects. Such knowledge is crucial for handling construction defect litigation, including lawsuits, claims, and mediation and arbitration efforts, thereby safeguarding the interests of all parties involved.
Understanding Construction Contracts and Warranties
Construction contracts act as a guide that details the obligations involved in remedying defects, and establishing a consensual procedure for their resolution. They delineate the extent of defect coverage, establish how long this coverage lasts, and elaborate on the steps to be followed when a claim arises.
Resolving Disputes and Litigation
Disputes, although frequently an undesirable element of construction projects, are typically resolved more amicably through other means than litigation. This approach not only saves time and money but also maintains business connections and provides a higher degree of control over the resolution process.
Through effective communication along with mediation techniques, parties can achieve seamless dispute resolutions within construction projects.
Leveraging Technology for Defect Management
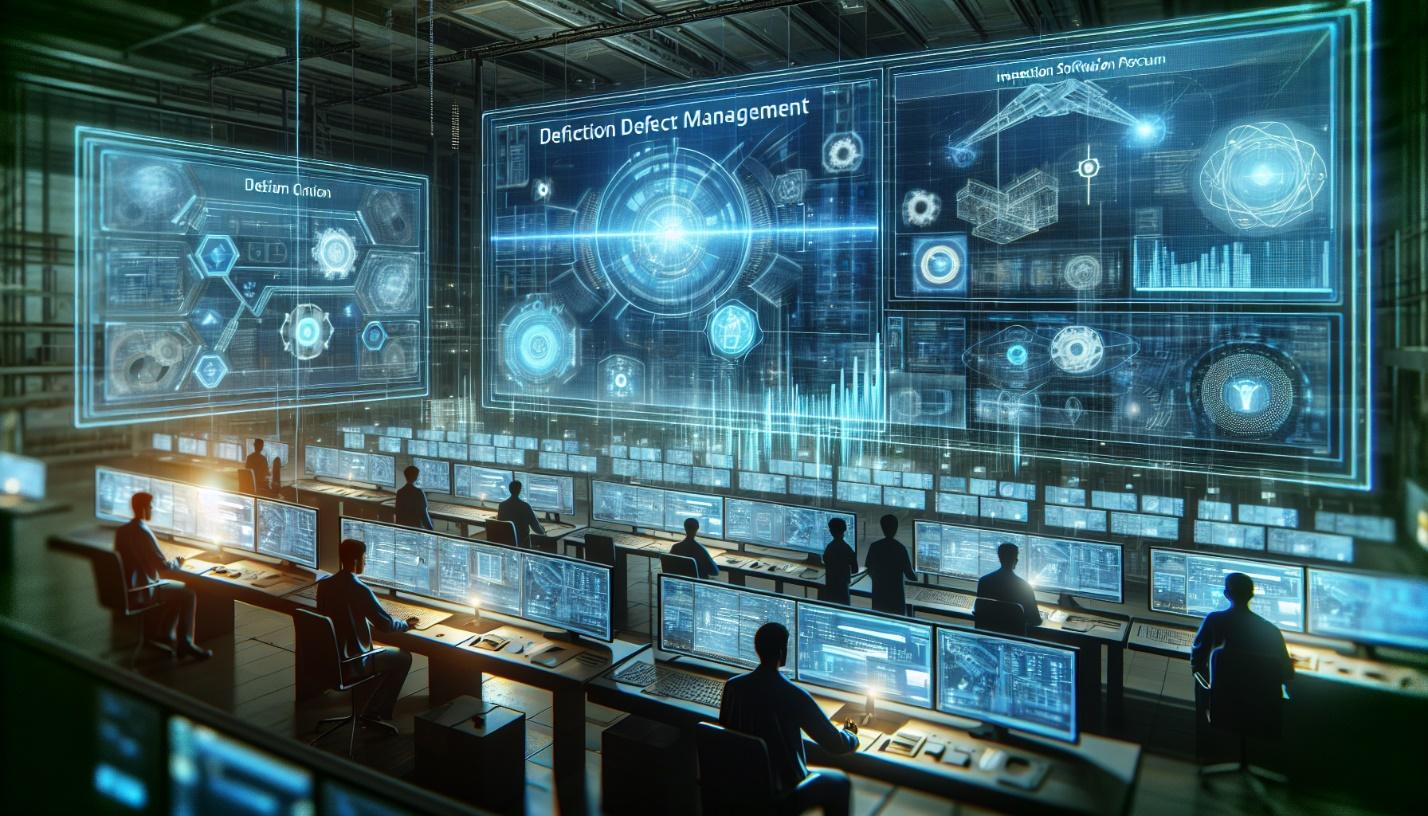
In today’s digital age, technology plays an instrumental role in overseeing and mitigating construction defects. Through the use of dedicated defect management applications, electronic documentation, and decisions informed by data analysis, technological advancements are improving the construction process by helping to avert potential defects.
Innovations in Inspection Software
Inspection software acts like an advanced technological tool, enhancing the efficiency of detecting and addressing flaws. It simplifies the workflow by:
- Making reporting methods more efficient
- Allocating duties to relevant parties
- Monitoring paperwork and progression closely
- Heightening precision and productivity in defect management.
Equipped with capabilities such as access to mobile devices and tailored inspection forms, this advancement is transforming the construction industry.
Digital Documentation and Reporting
Digital documentation serves as a complete log, meticulously recording every phase of the construction process. It provides visual proof that improves the clarity of reports and promotes effective communication between all parties involved in the project.
Data-Driven Decision Making
In our data-driven society, where data is likened to the new oil for its value in decision-making, analytics within the construction sector can guide knowledgeable choices and foresee possible deficiencies. This contributes to the efficient management of potential defects.
Summary
Maintaining the structural soundness of buildings involves thorough planning, the use of superior materials, strict implementation of quality control measures, and early detection and correction of construction defects. Recognizing key aspects that contribute to a building’s integrity, detecting construction flaws swiftly, acting on them immediately, and utilizing technology can help guarantee that our structures are secure, efficient, and resilient. As we construct future edifices with care and precision, let us commit to preserving their stature as enduring monuments for many years ahead.
Frequently Asked Questions
What are the pillars of building integrity?
Ensuring building safety and durability is fundamentally dependent on structural integrity, compliance with building codes, and the selection of high-quality materials. These critical factors play a pivotal role in averting construction defects and maintaining the robustness of constructions.
How can construction defects be identified?
Construction defects can be detected using various methods such as detailed visual examinations, expert evaluations, and sophisticated diagnostic instruments that may highlight indications like fissures, the buildup of moisture, or changes in surface color.
To avoid additional deterioration, it’s crucial to promptly tackle these problems.
Why is addressing construction defects important?
It is critical to tackle construction defects swiftly to maintain safety, avert additional harm, and safeguard financial investments.
To effectively deal with these problems, qualified contractors must be engaged for prompt detection and rectification.
What role does technology play in defect management?
The use of technology is vital in the management of defects as it enhances the process by simplifying how reports are made, allocating duties, monitoring paperwork and development, supplying comprehensive histories, and utilizing data analytics to guide more informed decisions within construction.
As a result of this integration of technology, resolving defects becomes more effective, which leads to an enhancement in quality across all aspects of construction.
What are the legal aspects of construction defects?
Understanding construction contracts, warranties, and the procedures for addressing defects is crucial for managing legal issues related to construction flaws effectively.
Often, disagreements and lawsuits about these matters are settled through peaceful methods such as mediation.
Key Takeaways
- Building integrity rests on three main pillars: structural soundness, adherence to building codes, and quality of materials, each fundamental for stability, safety, and durability.
- Construction defects can be identified through visual inspections and professional assessments, augmented by advanced diagnostic tools such as thermal imaging and drones for thorough analysis.
- Effectively addressing construction defects involves specific remediation for structural, water intrusion, and electrical/plumbing flaws, coupled with preventive measures and implementation of stringent quality assurance protocols.