Top Preventive Measures to Avoid Construction Defects
Seeking to prevent defects, expensive fixes, and legal complications stemming from construction issues? This write-up delves into strategies for circumventing such flaws in your building endeavors, emphasizing the importance of quality control, meticulous planning, and choosing appropriate materials. Adopt these measures to improve both the integrity and longevity of your construction projects.
Understanding Common Construction Defects
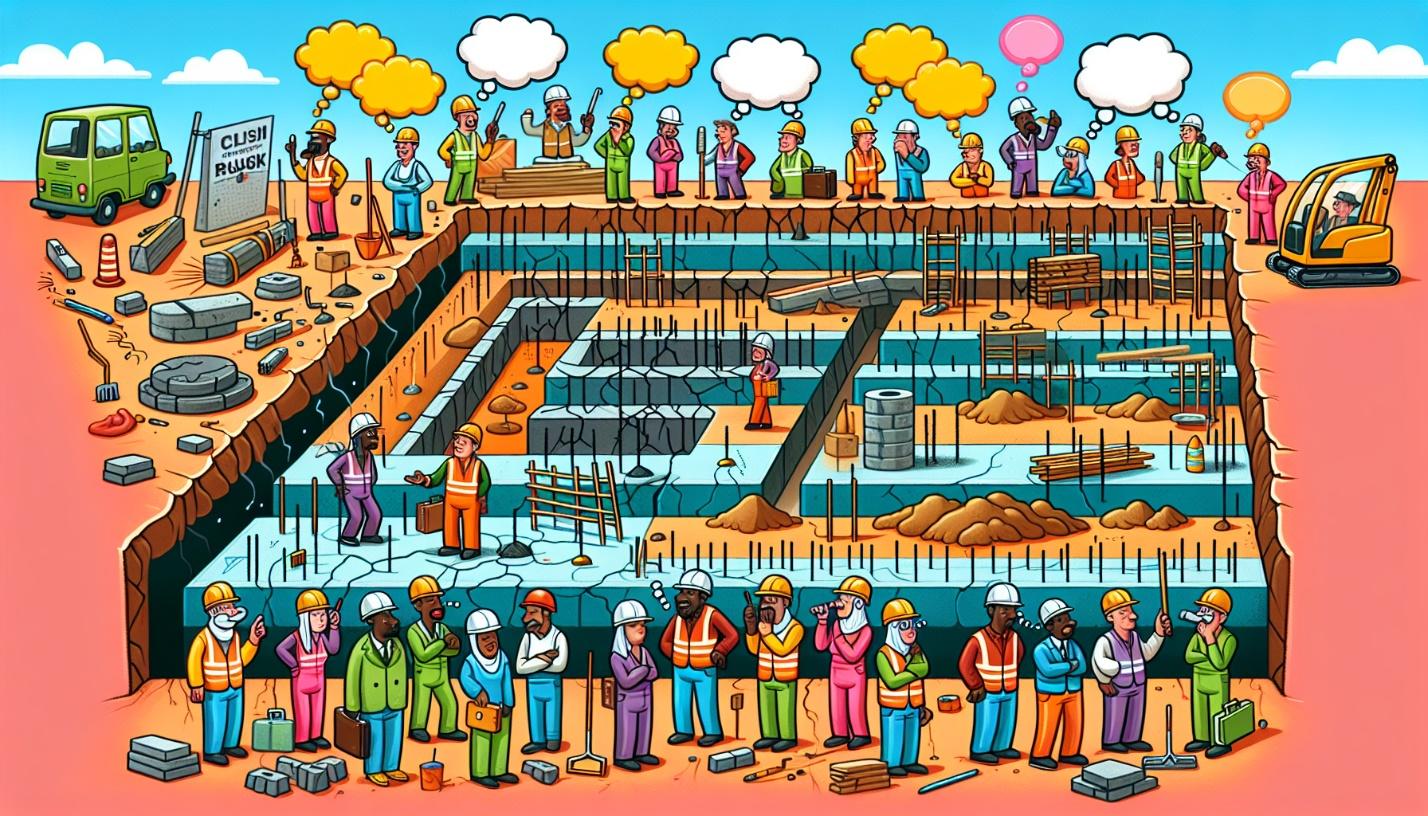
Defects in construction can range from superficial imperfections to grave structural issues. Issues such as foundation fractures, moisture penetration, and malfunctions in the heating, ventilation, and air conditioning systems frequently necessitate remedial action. Often originating from substandard quality control practices, incorrect installations or insufficient drainage setups contribute to these flaws during building projects. Acknowledging the various types of common defects is essential for minimizing potential risks and steering clear of expensive legal battles.
Effective communication and collaboration on the construction site are vital for defect detection and resolution. Fostering a collaborative culture among subcontractors, site managers, and project owners can significantly reduce defective workmanship and materials by quickly addressing any doubts or issues related to building plans.
Swiftly identifying any building defects throughout the stages of a construction project is crucial to halt their progression into larger concerns. For example, unattended water infiltration may lead to harmful mold development or even cause extensive damage to structures. Similarly overlooked foundation cracks could endanger the integrity of a structure presenting significant safety hazards.
Recognizing early indications of such faults and comprehending their underlying reasons allows those overseeing construction tasks - notably managers - to formulate proactive measures that effectively reduce construction-related deficiencies, thus promoting uninterrupted progress on site and enhancing overall build quality.
The Role of Quality Control in Construction
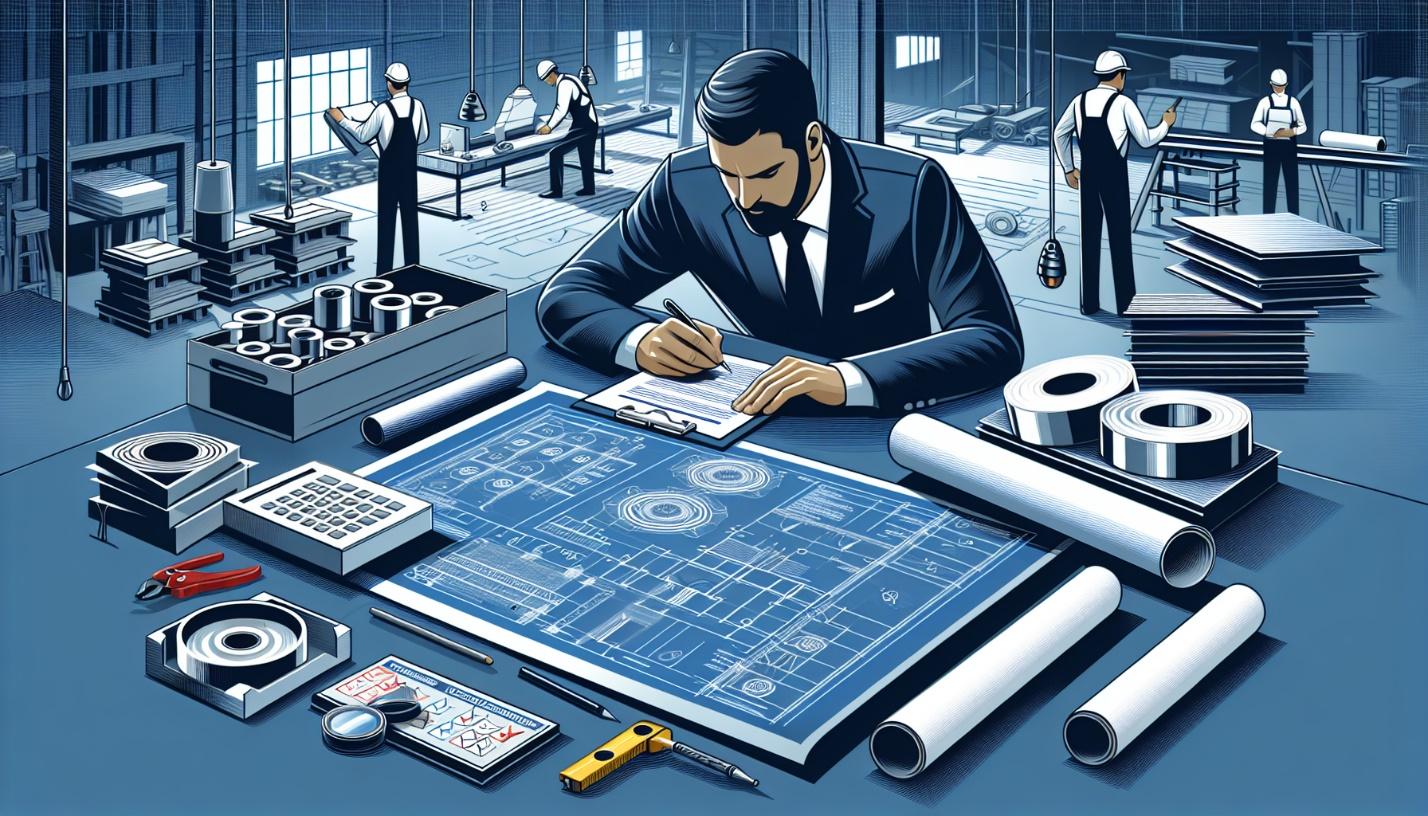
In the construction industry, quality control is a critical pillar for any project’s success, as it ensures that all outcomes are in line with both client demands and regulatory requirements. By conducting regular inspections at various stages of the construction process, it is possible to preserve high standards of quality while adhering to clients’ specifications. These evaluations enable timely detection and rectification of issues before they escalate into more significant complications, thus safeguarding against potential defects being overlooked due to an absence of thorough oversight mechanisms.
For a robust approach towards maintaining quality on-site, construction managers need to consistently observe not only the ongoing work but also scrutinize the materials utilized within each phase. Addressing shortcomings immediately when they surface lies at the core of adept management practices aimed at upholding superior project caliber—this active engagement plays a pivotal role in averting common setbacks such as cost overruns and time delays frequently encountered across construction projects.
Lastly, reinforcing these efforts is the indispensable function played by quality assurance processes which set out foundational expectations for excellence throughout every facet of a building endeavor’s duration—from commencement until conclusion. While concentrating on defect mitigation during actual operations falls under quality control purview. Assuring consistent adherence through predesignated benchmarks pertains directly to Quality Assurance protocols—the combination resulting in completed works that not only achieve but potentially surpass anticipated performance criteria hence delivering overall satisfaction amongst invested parties involved.
Importance of Thorough Planning and Accurate Design
Meticulous planning and precision in design are crucial for the success of construction projects. By setting precise specifications, confusion is eliminated, which leads to clear responsibilities and standards. Compliance with building codes is essential in guaranteeing that construction projects meet safety and quality requirements since these regulations are established to maintain public health and safety. Construction projects that keep their building drawings up-to-date can greatly reduce instances of construction defects.
Thorough planning and accurate design can significantly reduce construction defects by addressing potential issues early in the project lifecycle.
The adoption of cutting-edge technology like Augmented Reality (AR) and Virtual Reality (VR) has proven beneficial during the planning and designing stages. These technologies enhance visualization capabilities and communication among team members, minimizing chances for mistakes or gaps within the construction plans. AR’s simulation capabilities give designers a preview into potential challenges, allowing them to proactively address issues before they escalate, improving overall project delivery.
Neglecting proper planning or executing flawed designs can compromise the integrity of a structure significantly over time. Resulting from not adhering to code compliance or reaching expected performance levels among other things—thus increasing susceptibility toward defects in buildings’ constructions down the line if ignored at the initial stage whose solid foundation rests on prudent selections pertaining to both materials used as well as individuals involved in the process itself.
A focus on rigorous planning combined with exactitude in design helps ensure not only adherence but elevation beyond existing quality benchmarks, ensuring the creation of more secure long-lasting built environments subsequently thereof.
Using High-Quality, Durable Materials
Selecting the appropriate construction materials is vital to the durability and integrity of a building. Adhering strictly to the materials listed in architectural plans can greatly diminish construction defects. Construction contracts can specify the use of high-quality materials to prevent defects. Choosing durable, high-quality resources ensures not only an extended lifespan for buildings but also lowers potential expenses related to future repairs. For example, opting for materials resilient against harsh weather significantly decreases susceptibility to damage brought about by such conditions, thereby improving the overall quality of a structure.
Conversely, incorporating subpar materials may cause numerous deficiencies and long-term problems within constructions. Utilization of inferior concrete might lead directly to foundational instability marked by cracks or even major structural failures over time. Poor roofing choices could invite water penetration that promotes mold proliferation throughout a property.
Committing to superior quality in material selection effectively thwarts these complications from arising. As a result, it guarantees that structures are pleasing aesthetically while remaining sturdy and secure for occupants’ use and enjoyment.
Hiring Skilled Laborers and Ensuring Proper Training
Securing the services of well-versed and adept workers is pivotal for the triumphant execution of any construction project. Rigorous scrutiny when engaging subcontractors can confirm that high standards are met while diminishing potential flaws in workmanship. Laborers with experience and skill tend to comply more strictly with building specifications, thus reducing defect risks. They also have an aptitude for spotting problems at their inception and addressing them quickly, which contributes to uninterrupted progress on site.
It’s imperative that laborers receive comprehensive training to perform competently within a construction environment. Structured educational programs and official certifications prepare employees by endowing them with essential skills along with pertinent knowledge ensuring task efficiency along with adherence to safety protocols.
Specifically, educating those involved in construction about safeguarding techniques applicable during harsh weather conditions is vital for mitigating hazards present on-site. Committing resources toward thorough workforce education minimizes fault occurrences substantially and bolsters the superior caliber of the entire project.
Effective Project Management Techniques
Ensuring the success of a construction project and thwarting the occurrence of construction defects hinges on effective project management. Applying continuous improvement strategies is pivotal in uncovering and addressing quality issues as they emerge throughout the construction process. A well-crafted project management strategy, which factors in potential weather-related disruptions, plays an essential role in upholding timelines and averting setbacks.
Strategic planning is indispensable to prevent exorbitant cost escalations and extensive delays. Effective project management encompasses meticulous scheduling, budget control, and efficient utilization of resources—all critical components for ensuring that every phase of the construction process unfolds seamlessly. By meticulously orchestrating all elements associated with a building endeavor, construction managers are positioned to detect preventable defects early on thereby safeguarding steady progression through each stage.
Robust communication amongst stakeholders stands at the core of successful execution within any building initiative—a deficiency here can culminate in costly misunderstandings leading to compromised integrity within various structural facets. The cultivation of synergistic ties with code inspectors augments compliance efforts while enhancing overall results for your venture into development or renovation space. Proactively keeping abreast of storm patterns permits teams to enact protective measures that shield work against harmful effects posed by adverse weather conditions alike thus preserving ongoing operations without interruption where possible when Mother Nature takes unpredictable turns directionally wise fieldwork concerned.
It’s crucial not just to maintain adherence but also to remain continuously informed about changes related to guidelines pertaining to regional regulations governing how structures must be erected – deviance from these established parameters often leads down path-filled reworks resubmitting permissions both scenarios translating added expenses plus time lost due needless downtime spent correcting infractions found post hoc review cycle instead having been avoided first place had proper channels dialogue kept wide open during entire length duration current undertaking hand prior commencement breaking ground until final nail has driven last board position ending successfully completed chapter book labeled ‘Construction Project Management: A Guide Staying On Track While Maintaining High Standards’.
Compliance with Local Building Codes and Standards
Adhering to local building codes and standards is crucial for the assurance of both quality and safety in construction projects. Careful planning, along with meticulous design, plays a vital role in achieving compliance with these regulations, which are pivotal in safeguarding public health by shaping numerous aspects of construction including structural soundness and readiness for unforeseen events.
Failing to comply with established building codes can seriously compromise the integrity of a construction project. Such non-compliance may cause significant structural failures, pose serious safety hazards, and necessitate expensive corrective measures. Respecting these regulations is key not just to meeting but surpassing expected quality levels, thereby delivering structures that provide greater longevity as well as enhanced safety profiles.
Ongoing Maintenance and Periodic Inspections
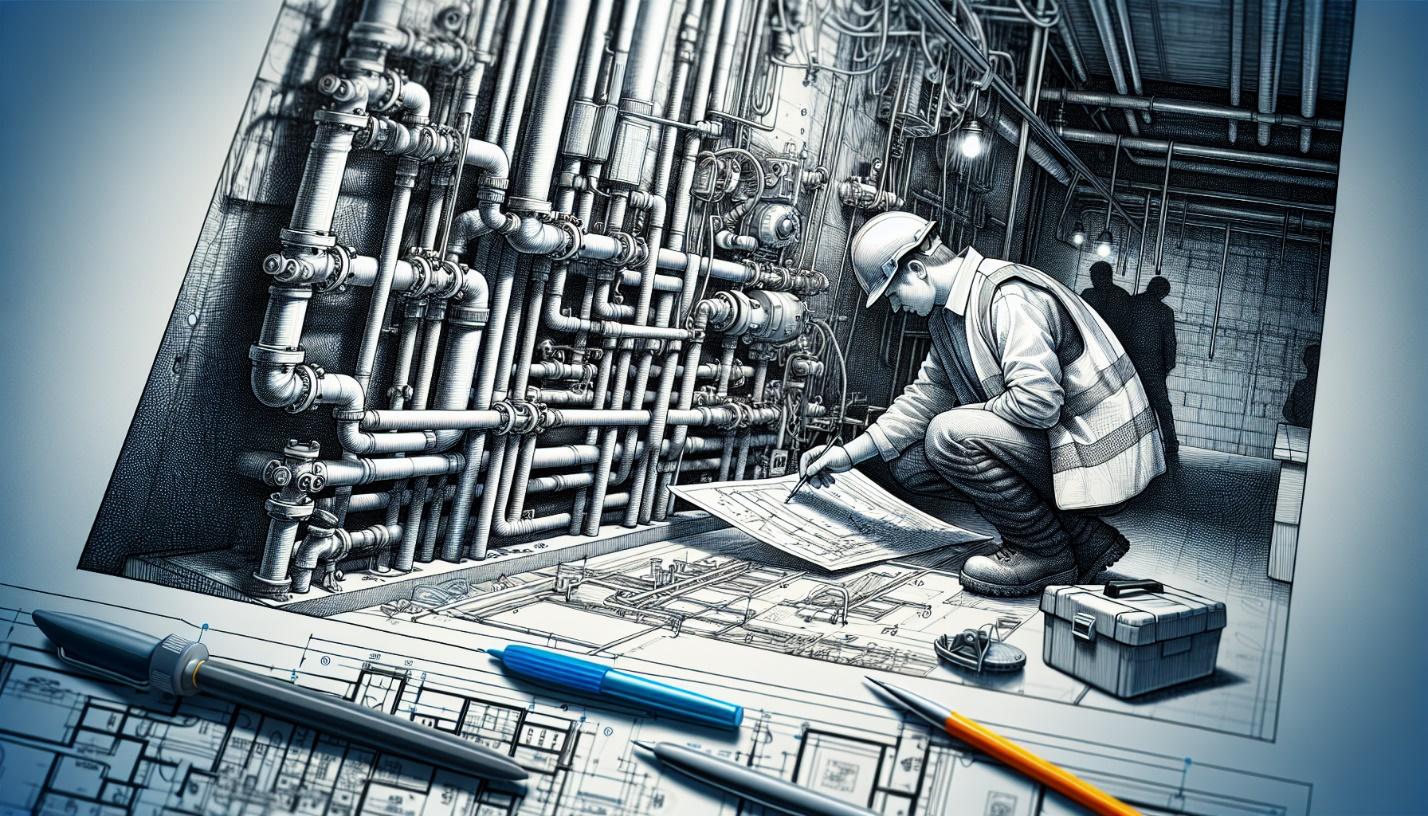
Maintaining a schedule of regular maintenance and conducting inspections at periodic intervals is essential for the early detection and rectification of potential problems during the construction process. Such inspections confirm that all systems within a building are operating as they should, which minimizes disruptions to service and improves operational efficiency. Addressing issues promptly through these checks helps avoid minor defects developing into more serious, expensive problems.
Having an inspection program that’s thoughtfully devised leads to fewer instances where equipment or systems are out of commission, thereby boosting overall performance levels. Consistent upkeep plays an indispensable role in increasing the longevity of buildings while ensuring their ongoing safety and effectiveness.
By putting into place a thorough regimen for both maintenance and inspections, one can greatly diminish chances for faults occurring—thus raising the standard of quality across completed projects.
Mitigating Environmental Factors
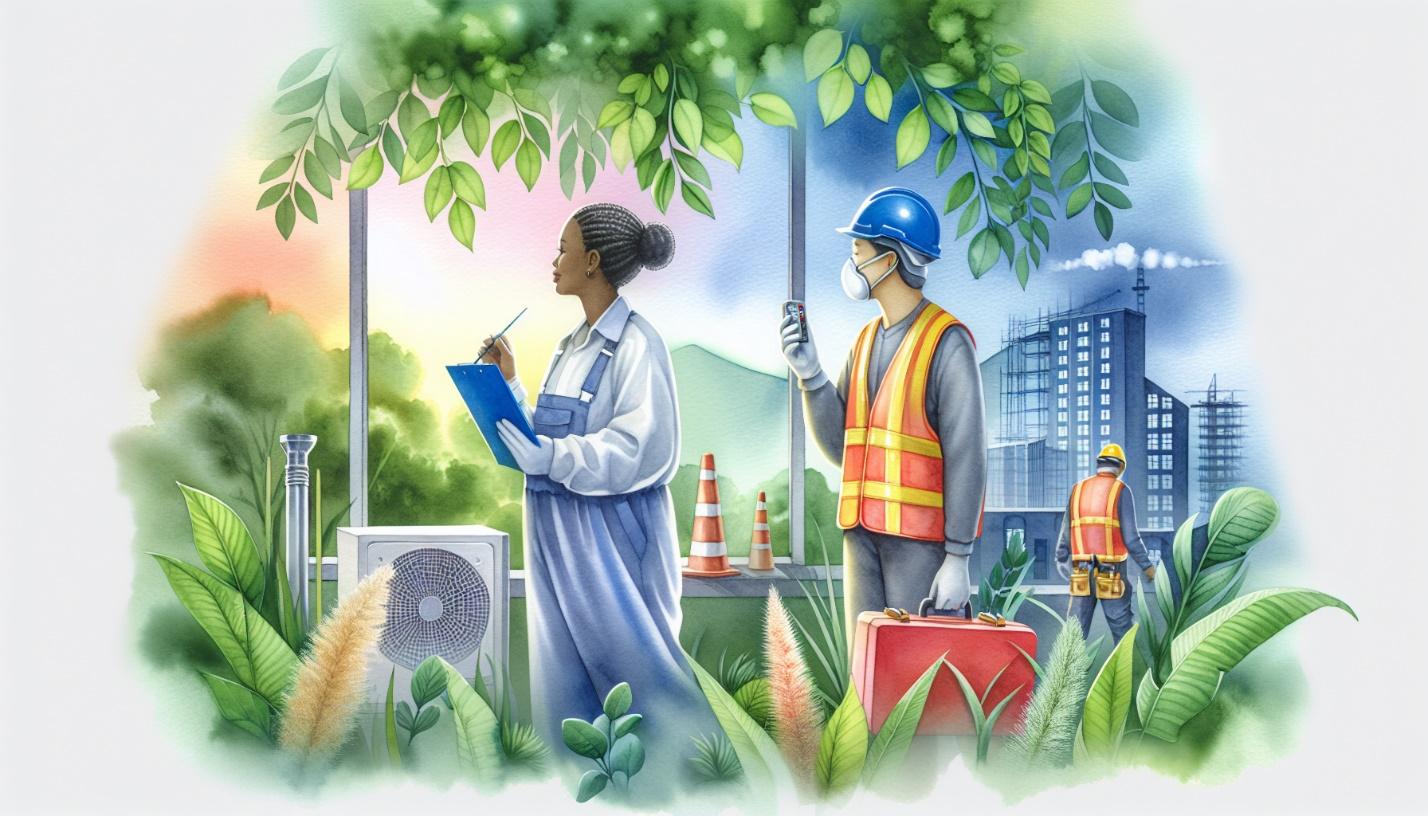
Environmental factors can significantly impact the quality and durability of construction projects. Adverse weather events like hurricanes and floods can cause significant damage to construction sites, leading to delays and increased costs. Implementing building designs that are resilient to climate impacts, such as elevated structures in flood-prone areas, can reduce the risk of damage.
Choosing weather-resistant materials can enhance the durability of buildings against extreme weather conditions. Incorporating landscape design elements, such as drainage systems, can mitigate flooding risks on construction sites. Taking these preventive measures reduces the impact of environmental factors on projects, ensuring smoother construction progress and higher quality outcomes.
Leveraging New Technologies and Innovations
Innovative technologies are pivotal in mitigating construction defects and improving the results of construction projects. Centralized digital platforms like Building Information Modeling (BIM) improve coordination and precision, leading to fewer mistakes and cost reductions during building phases. Drones aid surveying and oversight tasks by delivering enhanced accuracy and time efficiency.
The adoption of contemporary tools such as mobile devices refines inspection procedures while bolstering overall productivity. The application of technology for immediate environmental monitoring yields valuable insights that facilitate timely adjustments throughout the construction process.
By integrating these cutting-edge technologies into operations, quality control measures become more robust with streamlined automation and increased transparency of information — all contributing factors to superior project outcomes.
Case Studies of Successful Projects
Studying successful construction projects can provide valuable insights into best practices and effective strategies for defect prevention. For instance, a project that utilized high-quality materials, thorough planning, and regular inspections was able to minimize defects and achieve outstanding results. Such examples highlight the importance of comprehensive planning and quality control in construction projects.
Another successful case study involved a project that leveraged modern technologies like BIM and drones to enhance collaboration and accuracy. By integrating these technologies into their workflow, the project team was able to identify and address potential issues early, leading to a significant reduction in defects and cost savings. These real-world examples serve as practical guides for future projects, demonstrating how preventive measures can lead to successful outcomes.
Learning from successful case studies can positively influence future construction quality, helping project stakeholders replicate successes and avoid pitfalls. Applying the lessons learned from these projects enhances the quality and durability of their own projects, ensuring long-term success and client satisfaction.
Summary
To effectively combat construction defects, a comprehensive strategy is necessary, involving meticulous planning and adherence to quality control measures. This should include the selection of superior materials, employing adept workers, rigorous project management practices, strict compliance with building codes and standards, consistent upkeep of structures once built as well as taking advantage of innovative technologies in the field. Through these preventative steps taken by construction managers, construction managers can dramatically minimize potential flaws, which benefits not only the pace at which projects advance but also greatly improves their overall quality.
The ideas and approaches outlined within this article aren’t merely abstract concepts. They’re pragmatic solutions that have demonstrated success on actual construction sites. Construction managers who embrace these proven tactics stand to enhance both the structural integrity and longevity of their works—thereby delivering safer buildings more likely to achieve long-lasting success. We must endeavor toward constructing facilities that are not just robust but endure over time without faltering under pressures or challenges they may face.
Frequently Asked Questions
What are common examples of construction defects?
Typical instances of construction defects encompass issues like cracks in the foundation, water penetration, problems with HVAC systems, and failures in materials. These often stem from inadequate quality control during building along with incorrect installation processes.
It is essential to tackle these problems swiftly to maintain both the durability and security of a building.
How does quality control help in reducing construction defects?
Regular inspections and prompt rectifications as part of the quality control measures significantly minimize construction defects, ensuring that both client expectations and regulatory standards are met. By taking this proactive stance, high-quality outcomes are consistently upheld during the construction process.
Why is thorough planning and accurate design important in construction?
In the field of construction, meticulous planning and precise design play essential roles in reducing the likelihood of flaws and guaranteeing compliance with building codes. These practices promote improved communication, heightened responsibility, and as a result, superior results for projects.
What role do high-quality materials play in construction projects?
Utilizing specified materials of high quality is crucial in ensuring the safety and durability of construction projects. This approach helps to minimize defects, thereby reducing future repair costs and mitigating serious risks such as water infiltration and foundation cracks.
How can new technologies help in preventing construction defects?
Innovations like Building Information Modeling (BIM), the use of drones, and mobile technology are instrumental in curtailing construction defects. They foster better teamwork, augment precision in construction processes, and allow for the early detection of potential issues.
The adoption of these modern tools promotes more streamlined inspections and reinforces quality control measures. This results in a reduction of mistakes during the building phase and leads to significant cost savings.
Key Takeaways
- Understanding and identifying common construction defects early can prevent serious issues and costly repairs.
- Implementing strict quality control measures, along with thorough planning and compliance with building codes, is essential for successful construction outcomes.
- Leveraging new technologies and ongoing maintenance can enhance project quality, reduce defects, and improve overall efficiency in construction.